Mixed mode fracture behavior of a multi-directional laminate composite produced by a wet layup
Keywords:
Composite Materials, CFRP, Minxed-Mode, Fracture Toughness, Stress Intensity Factors, Brazilian Disk Specimens, DCB, C-ELS, MMELS, Fracture ResistanceSynopsis
Carbon fiber reinforced polymers are used for improving performance and lowering operational costs of structures, particularly in the aerospace industry. However, lack of knowledge of the fracture behavior of these composites may result in catastrophic disasters. Understanding delamination initiation and propagation of carbon fiber reinforced polymer laminates (CFRPs) may assist in preventing catastrophic failures of structures such as airplanes. Precise engineering tools may lead to safer design, improved performance, as well as lowered operational costs of structures constructed from these materials.
This study focuses on a delamination between two fiber reinforced composite plies. The upper ply is a UD fabric with fibers oriented in the 0o- direction and the lower ply is a plain balanced weave with tows oriented in the +45o/-45o - directions. The composite is manufactured by a wet-layup process.
Twenty-seven successful mixed mode fracture toughness tests were carried out using Brazilian disk specimens to determine the fracture toughness properties of this composite and interface. During each test, a load P was applied at an angle omega with respect to an artificial delamination located between the investigated plies. Seven loading angles were used to achieve different mixed mode combinations. Based on the results, using finite element analyses in conjunction with the three-dimensional conservative interaction energy integral or M-integral and the displacement extrapolation method, the stress intensity factors resulting from mechanical loads, as well as residual curing stresses were obtained along the delamination front for each specimen. The stress intensity factors were superposed and used to calculate the interface initiation energy release rate and mode mixities or phase angles. Finally, two and three-dimensional failure criteria were proposed for this material and interface and a statistical analysis with a 10% probability of unexpected failure in the safe zone with a confidence of 95% was performed. The failure curves and surfaces may be used to predict catastrophic failure for this material and interface, as well as to lead to a better understanding of interlaminar delamination.
Initiation and propagation properties were determined based on nearly mode I, nearly mode II and mixed mode fracture toughness and fracture resistance tests. For mode I, DCB tests, which were performed and described in Chocron and Banks-Sills (2019), were reanalyzed. For the nearly mode II and mixed mode initiation and resistance properties, C-ELS and MMELS fracture tests were performed, respectively, and analyzed. These tests were quasi-static and consisted of two stages. In the first test stage, an artificial delamination was extended and in the second test stage, propagation from a natural precrack was observed.
The experimental and numerical results obtained from the tests were employed to determine the fracture resistance GiR-curves for nearly mode I, nearly mode II and for one mixed mode I/II deformation ratio. The GiR-curves were generated by means of a local M-integral approach, as well as by means of the global experimental compliance method (ECM) and included determination of the initiation Gic and steady-state propagation Giss values. The GiR-curves obtained using both methods were compared for each tested specimen. In addition, the phase angles psi and phi which define the mode mixities, were calculated for each specimen and test.
The R-curves found may be used to account for the fracture resistance energy release rate required for propagation and to assist in improving the design and safety of a structure made of this laminate with this interface.
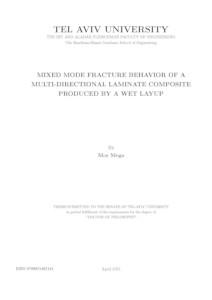